The Development of Steel Marking Processes: Innovations and Applications
The world of metal stamping procedures has actually seen a transformative trip noted by constant technology and adaptation to fulfill the demands of modern commercial practices. From the standard techniques deeply rooted in background to the innovative technologies driving high-speed accuracy, the development of steel stamping has actually been nothing except remarkable. As brand-new tooling methods and automation find their method into this market, the implications for effectiveness and top quality are profound. The applications extend throughout a range of industries, each profiting uniquely from the developments in steel stamping processes.
Typical Metal Stamping Methods
Typical steel stamping techniques have long been the foundation of making processes in various markets due to their effectiveness and accuracy. The procedure entails forming a metal sheet or coil right into a desired shape by pressing it between a die and a punch. This technique is extensively made use of for creating large quantities of parts with high precision at a rapid pace.
One of the essential advantages of standard steel stamping methods is the capability to keep limited resistances, making certain that each component fulfills the called for requirements continually. This level of accuracy is important in industries such as automobile, aerospace, and electronics, where also small inconsistencies can lead to considerable problems.
Furthermore, conventional metal marking strategies use cost-effective services for automation contrasted to various other producing methods. The ability to mark components in fast sequence lessens production time and reduces labor prices, making it an appealing choice for businesses wanting to optimize their production processes.
Emergence of High-Speed Stamping
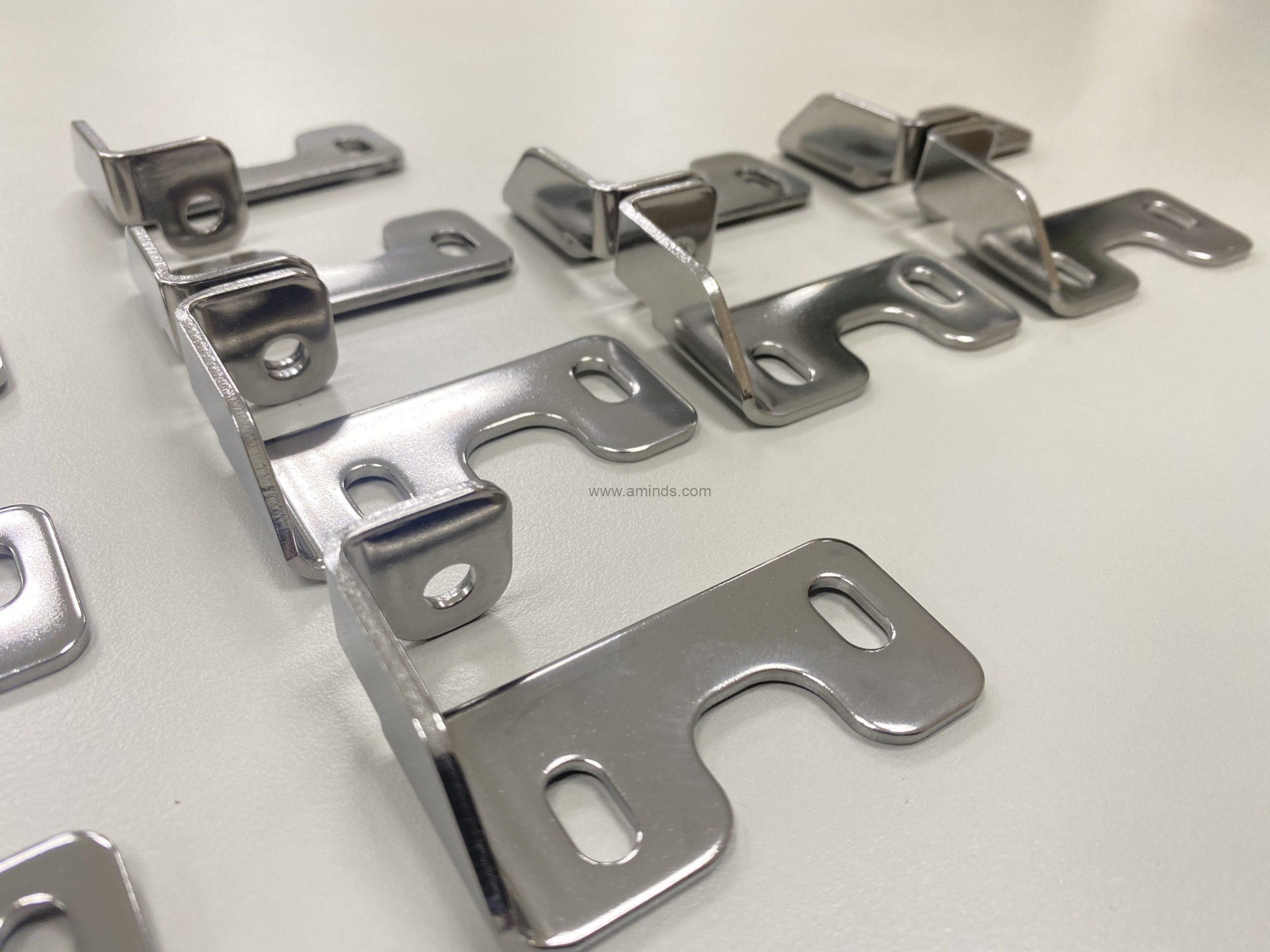
One of the crucial advantages of high-speed stamping is its ability to keep precision and consistency also at accelerated handling speeds. This precision is crucial in markets where tight tolerances and detailed designs are needed. Additionally, high-speed stamping permits the handling of a vast array of products, including aluminum, stainless-steel, and copper, further expanding its navigate to these guys applicability across numerous industries.
In addition, the emergence of high-speed stamping has actually made it possible for producers to satisfy the expanding demand for complicated parts in industries such as automobile, aerospace, and electronics (Metal Stamping). By leveraging the rate and precision of high-speed marking innovation, firms can boost their competitiveness in a rapidly progressing market landscape
Innovations in Tooling Technology
With the evolution of high-speed marking enabling enhanced precision and efficiency in metal forming processes, the field of metal stamping has seen considerable improvements in tooling modern technology. Tooling modern technology plays an essential role in metal stamping operations, influencing factors such as product quality, production rate, and total cost-effectiveness. One vital development in tooling modern technology visite site is the advancement of smart tooling systems that integrate sensors and keeping track of devices to offer real-time data on the stamping process. These systems can detect issues such as device wear or imbalance, enabling for instant adjustments to maintain optimal efficiency.
By making use of these advanced materials, tooling makers can generate dies and mold and mildews that withstand the high pressures and temperatures included in steel marking procedures, resulting in longer tool life and better production efficiency. In general, these improvements in tooling modern technology have transformed the metal stamping industry, permitting suppliers to accomplish greater degrees of accuracy, productivity, and cost financial savings.
Assimilation of Automation in Marking
As automation remains to reshape see this page the landscape of steel stamping procedures, the integration of automated systems has come to be increasingly common in modern manufacturing facilities. Automated systems offer numerous benefits in steel stamping, consisting of boosted performance, enhanced precision, and improved safety. By incorporating automation into stamping processes, manufacturers can reduce cycle times, decrease product waste, and enhance production throughput.
Among the key components of automation in marking is making use of robot arms for jobs such as material handling, component manipulation, and top quality examination (Metal Stamping). These robot systems can carry out repetitive and labor-intensive jobs with speed and accuracy, freeing up human drivers to focus on even more complicated operations. In addition, automation enables for real-time surveillance and modification of marking processes, leading to higher overall procedure control and quality guarantee
Furthermore, the assimilation of automation in stamping allows manufacturers to accomplish consistent component quality, satisfy limited tolerances, and improve total efficiency. As modern technology proceeds to development, the duty of automation in metal marking procedures is expected to broaden better, driving development and efficiency in the manufacturing market.
Applications Across Diverse Industries
Integrating metal marking procedures across varied sectors showcases the adaptability and versatility of this manufacturing strategy. Furthermore, the appliance sector advantages from metal marking processes to manufacture components for refrigerators, washing makers, and other household devices. The adaptability of steel stamping procedures makes it a beneficial manufacturing technique throughout various sectors, demonstrating its relevance in contemporary production procedures.
Final Thought
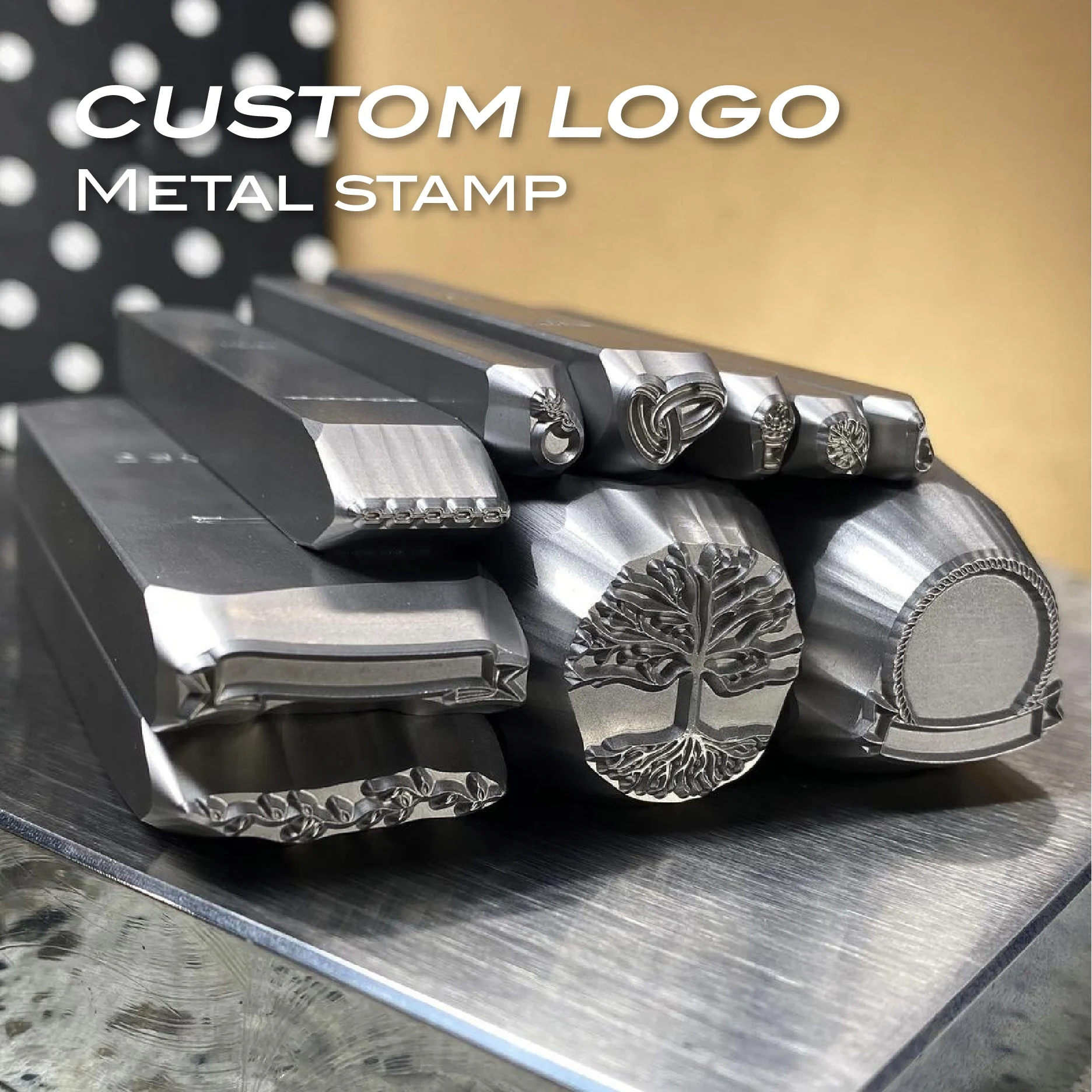
Comments on “Metal Stamping Procedures: From Prototyping to Mass Production”